As part of the Engineering and Design team at Saringer Life Science Technologies, I played an important role in the redesign of the Venowave. The Venowave is a patented medical device designed to improve circulation and prevent deep vein thrombosis (DVT).
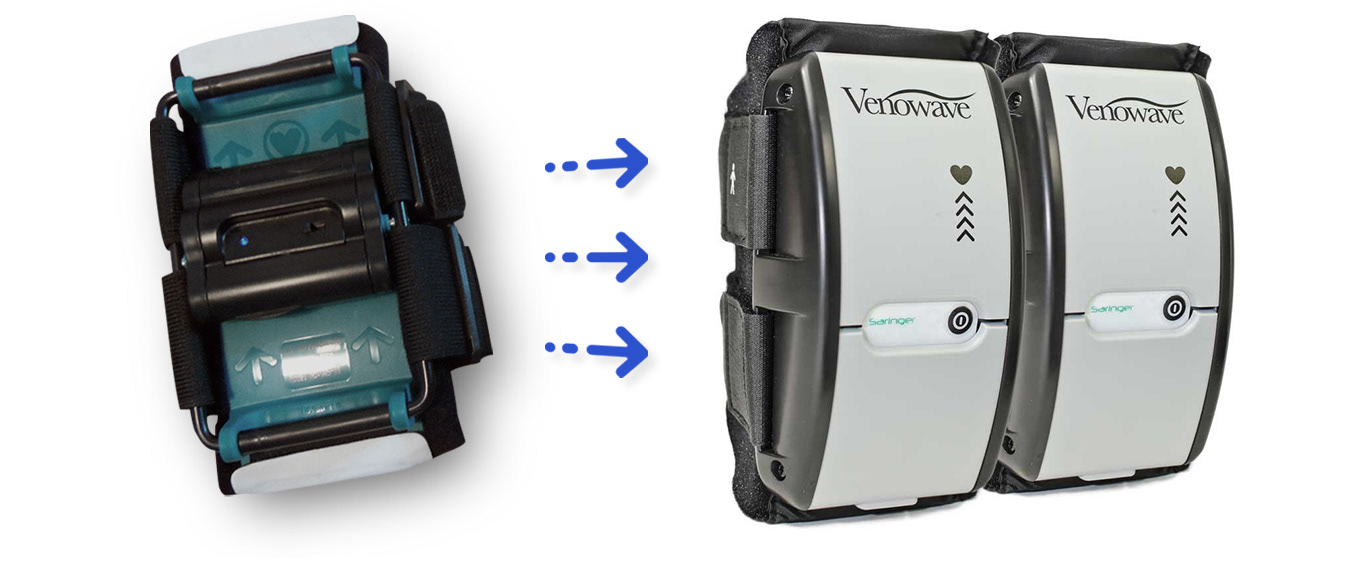
When I joined this project, the technology had already been developed and patented but the product presented some problems that needed to be addressed:
1. Difficult to put on and take off (Help from someone else needed in most cases)
2. Hard to clean and disinfect
3. Exposed moving parts presented some risk to the user
4. Unappealing appearance
5. Short battery life
6. Short product life
7. Manufacturing cost-efficiency needed improvement
8. Documentation compliant with ISO 13485 was needed
My Role
I was responsible for the mechanical design of all components for the new Venowave assembly, as well as, managing the design of all electronic and firmware components for this product. I was also responsible for managing the product's bill of materials and its manufacturing overseas.
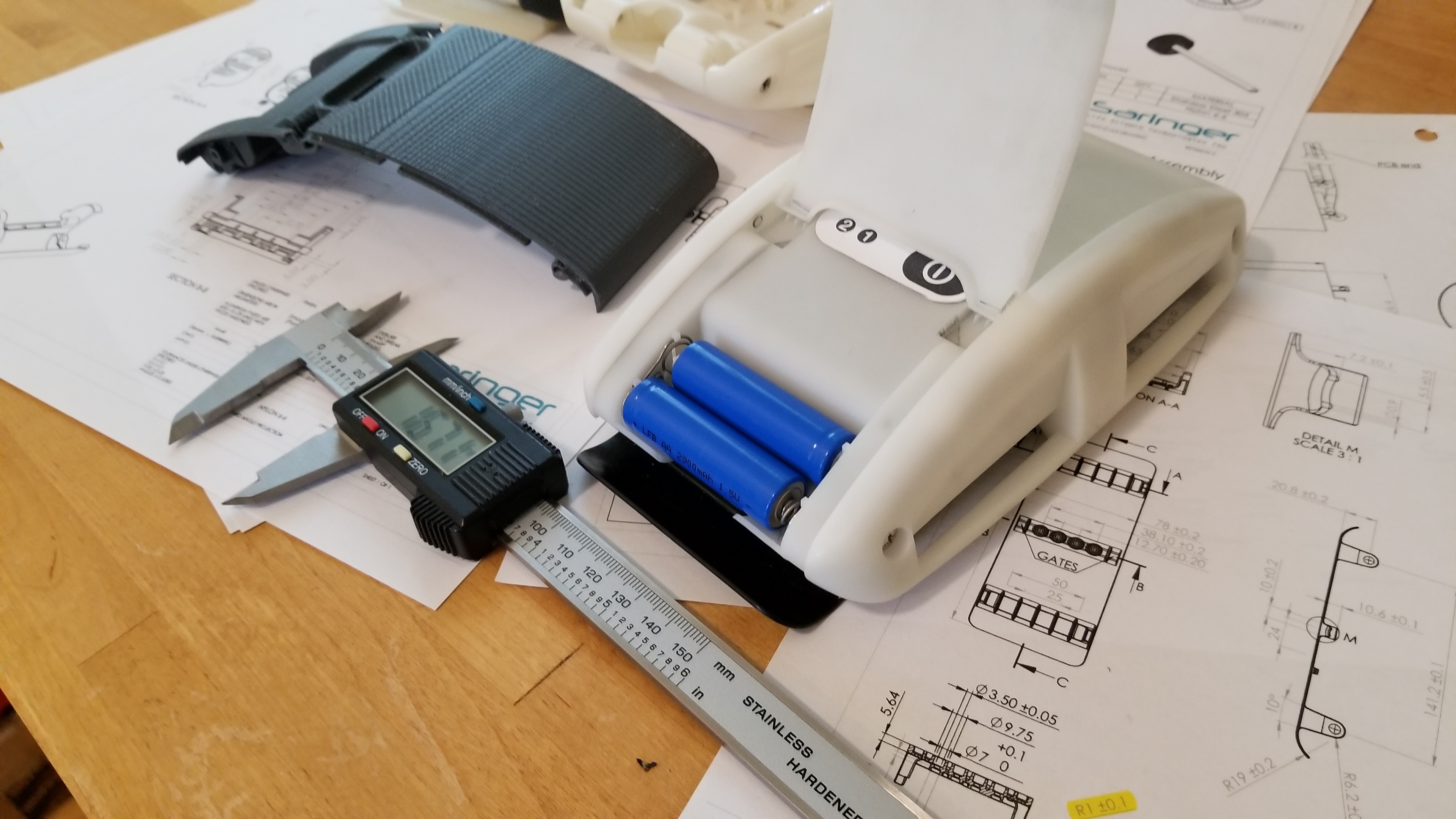
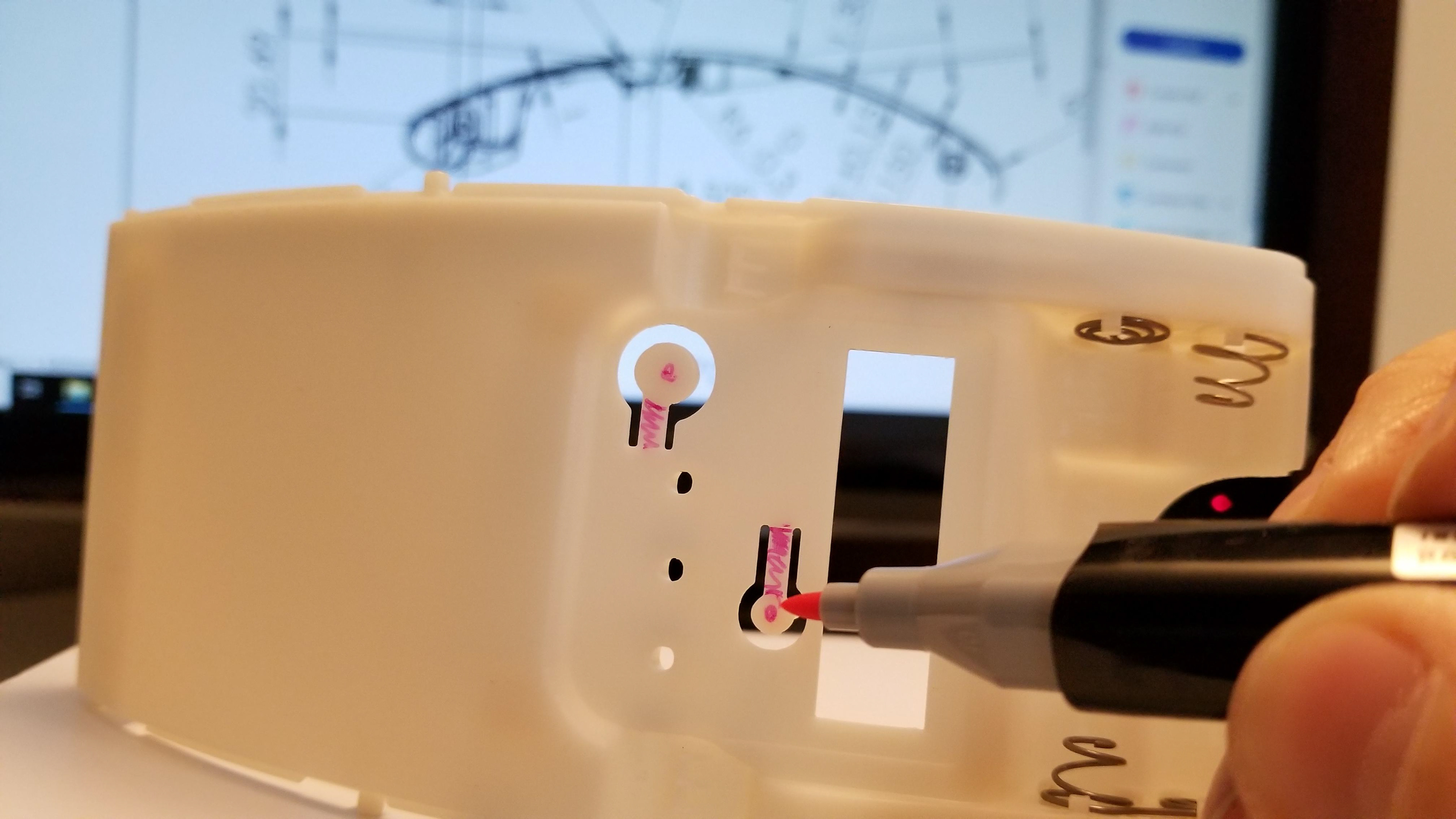
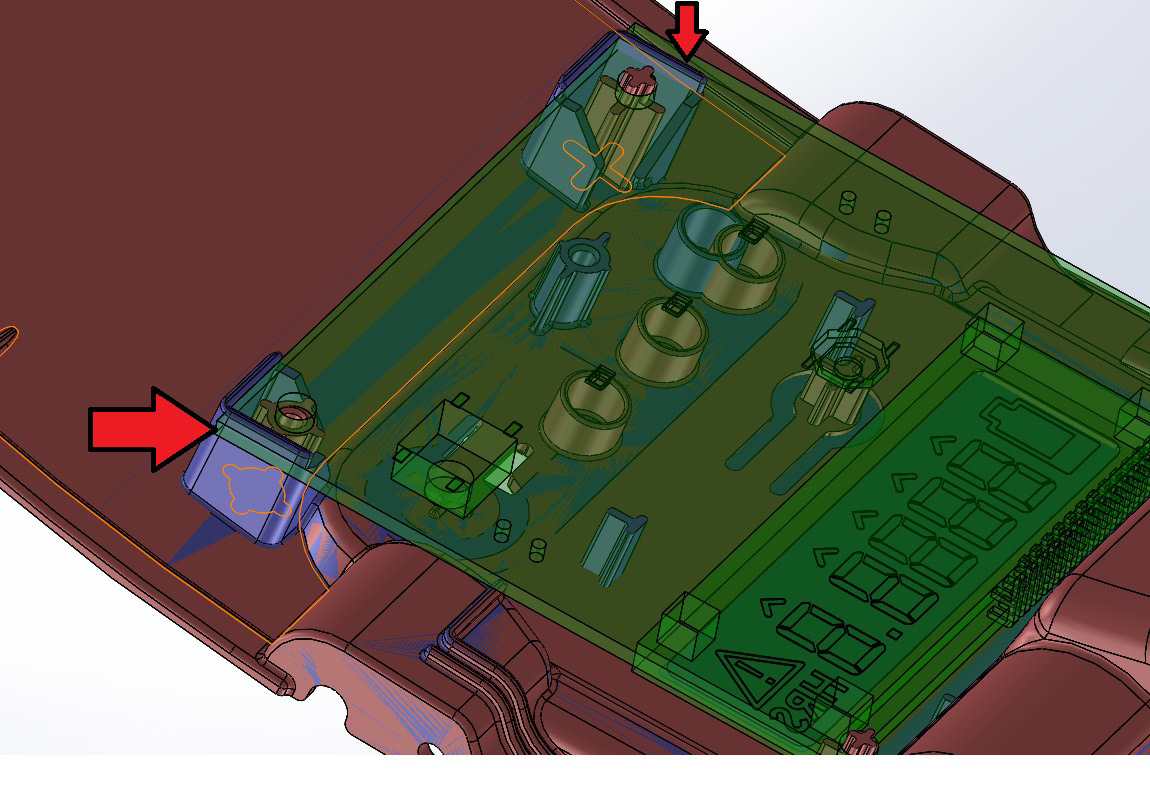
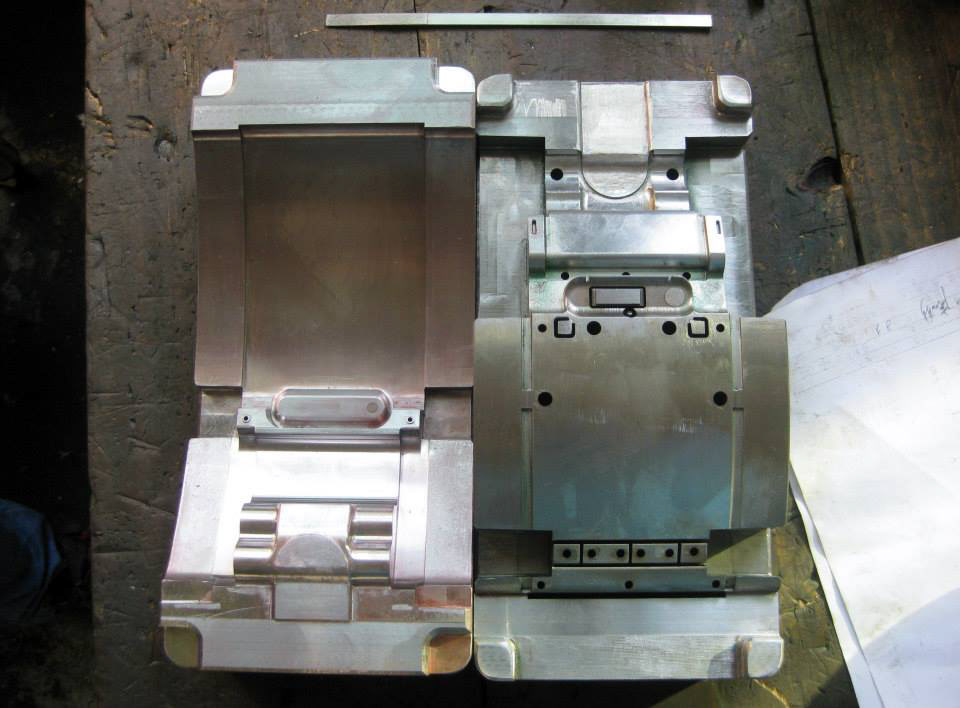
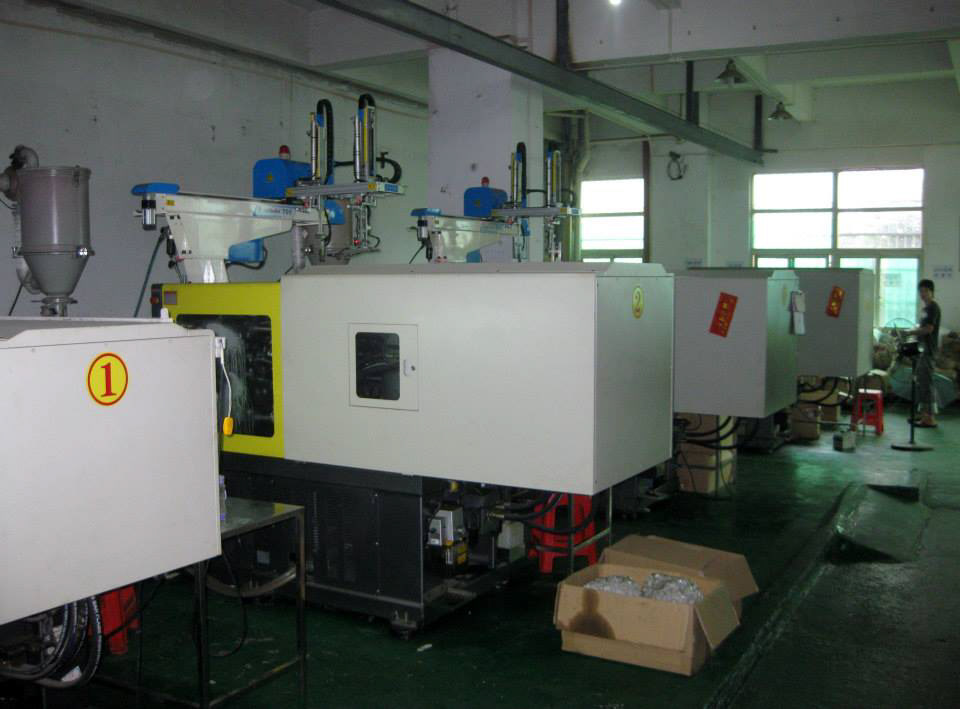
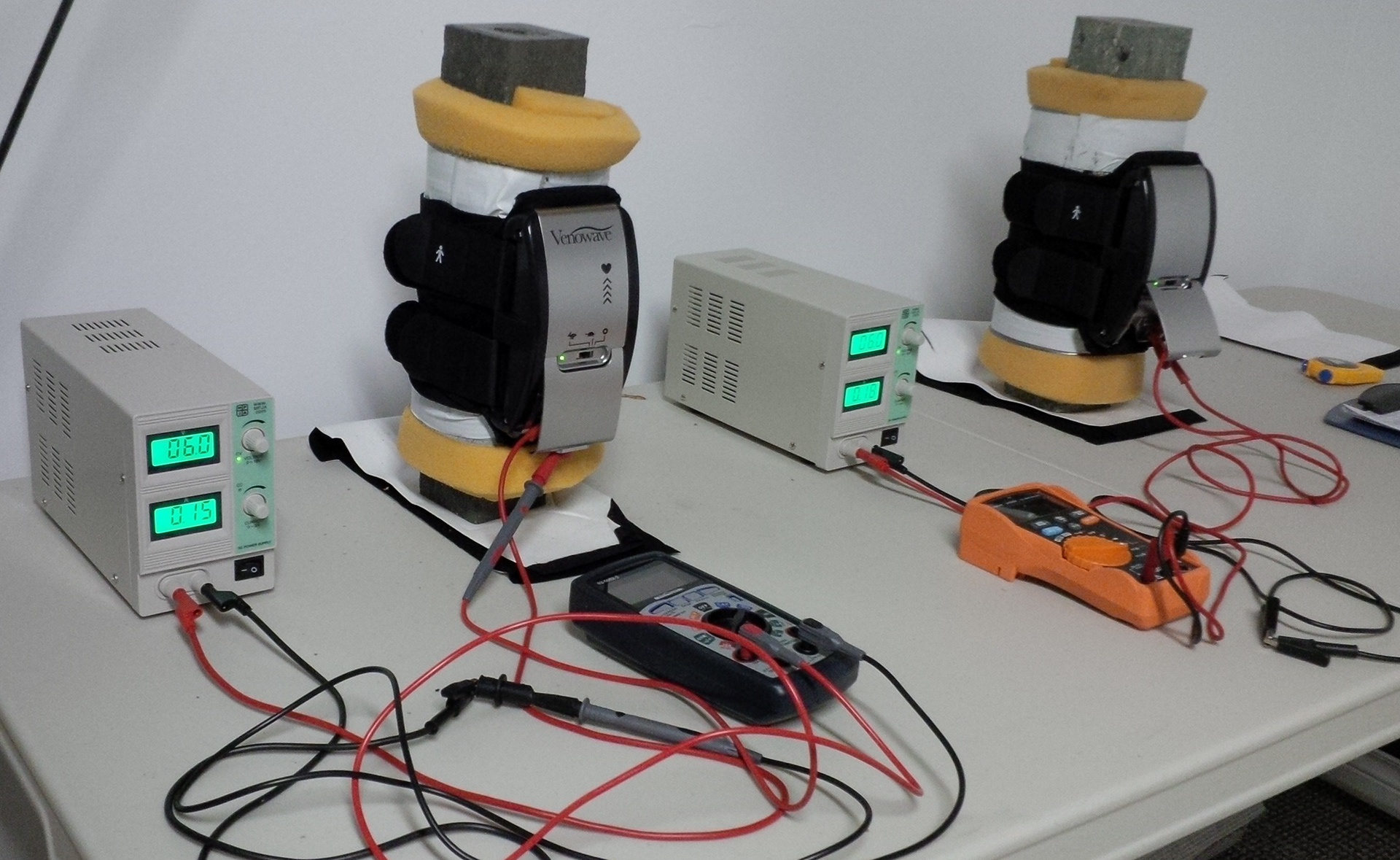
New Design
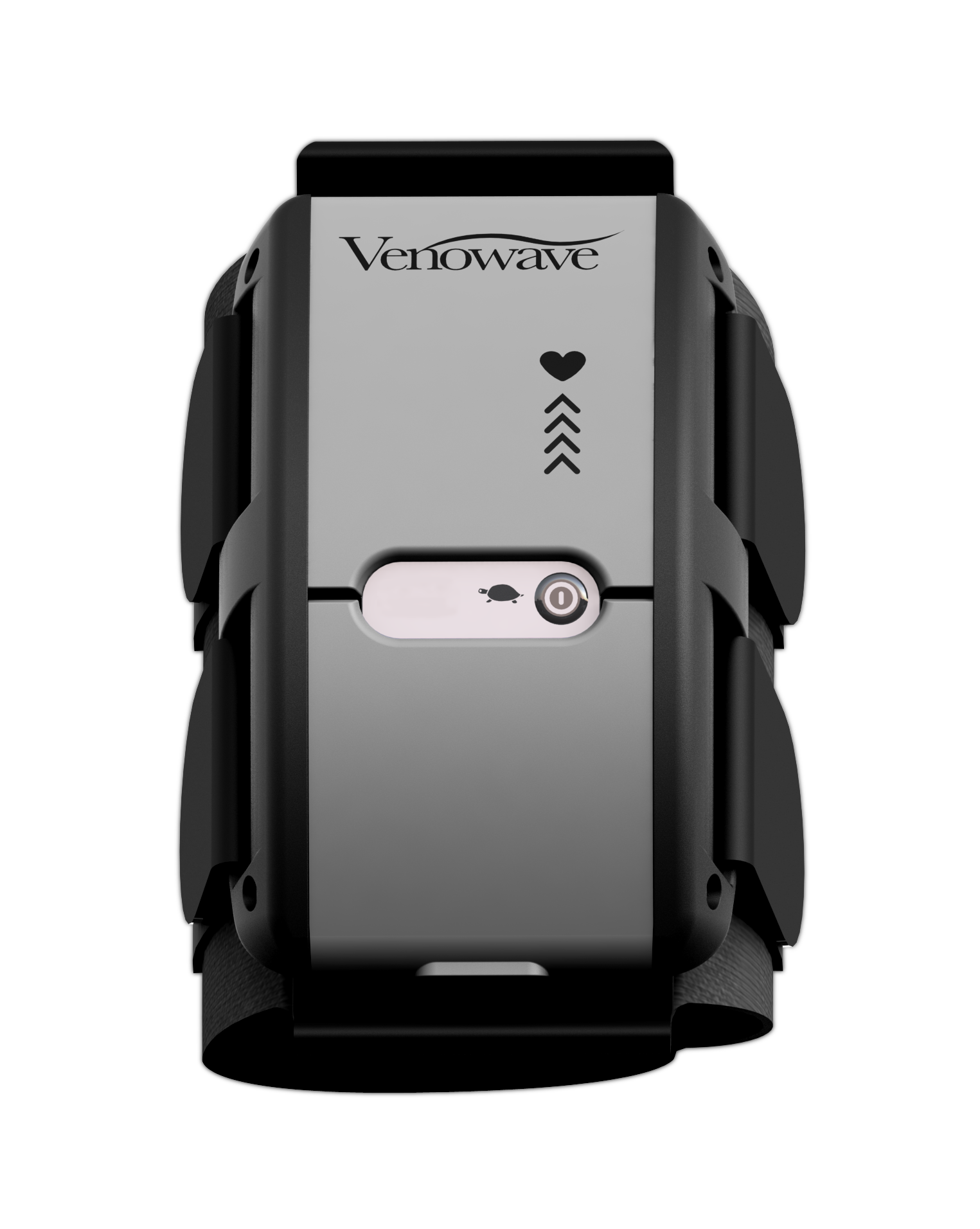
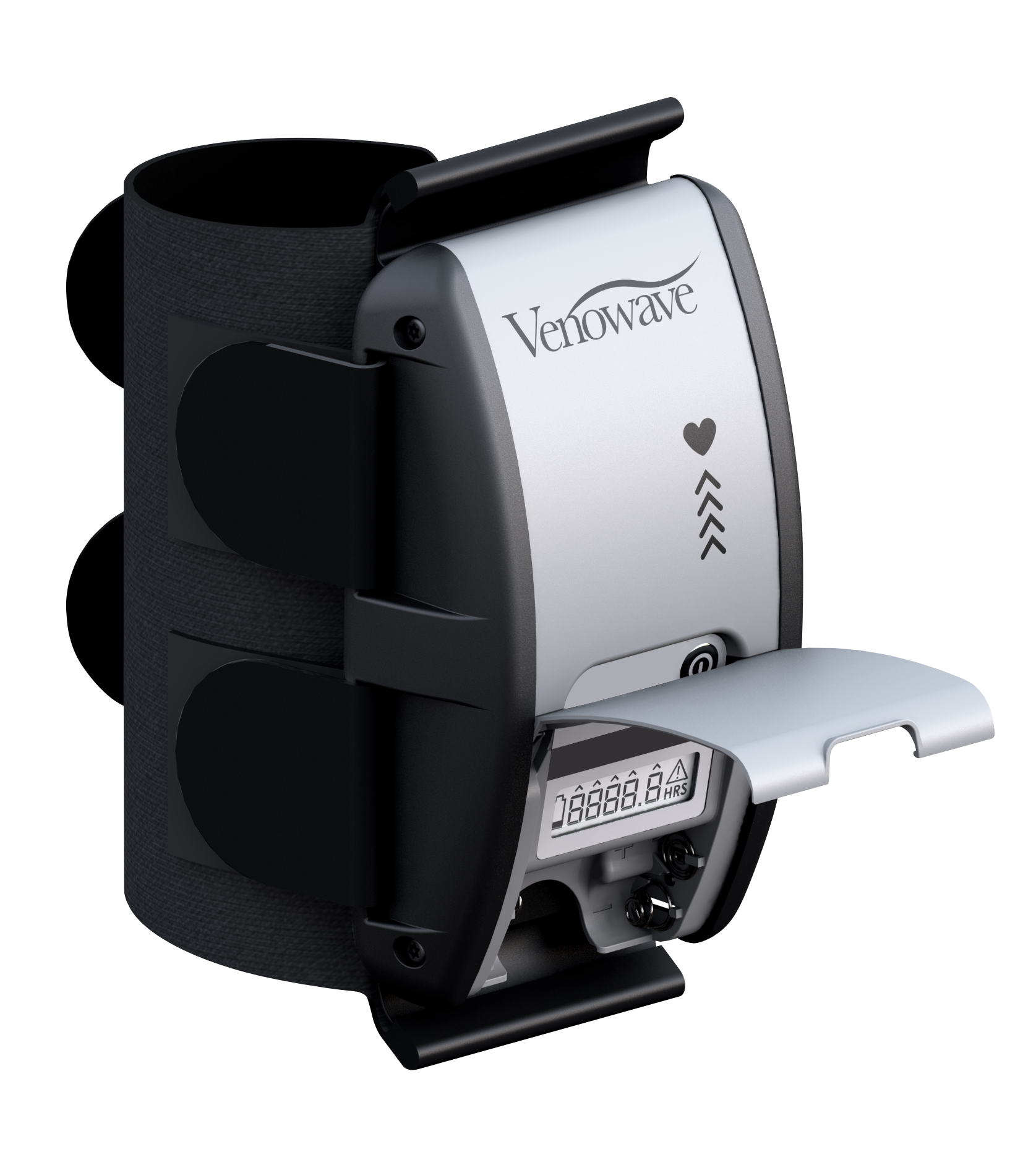
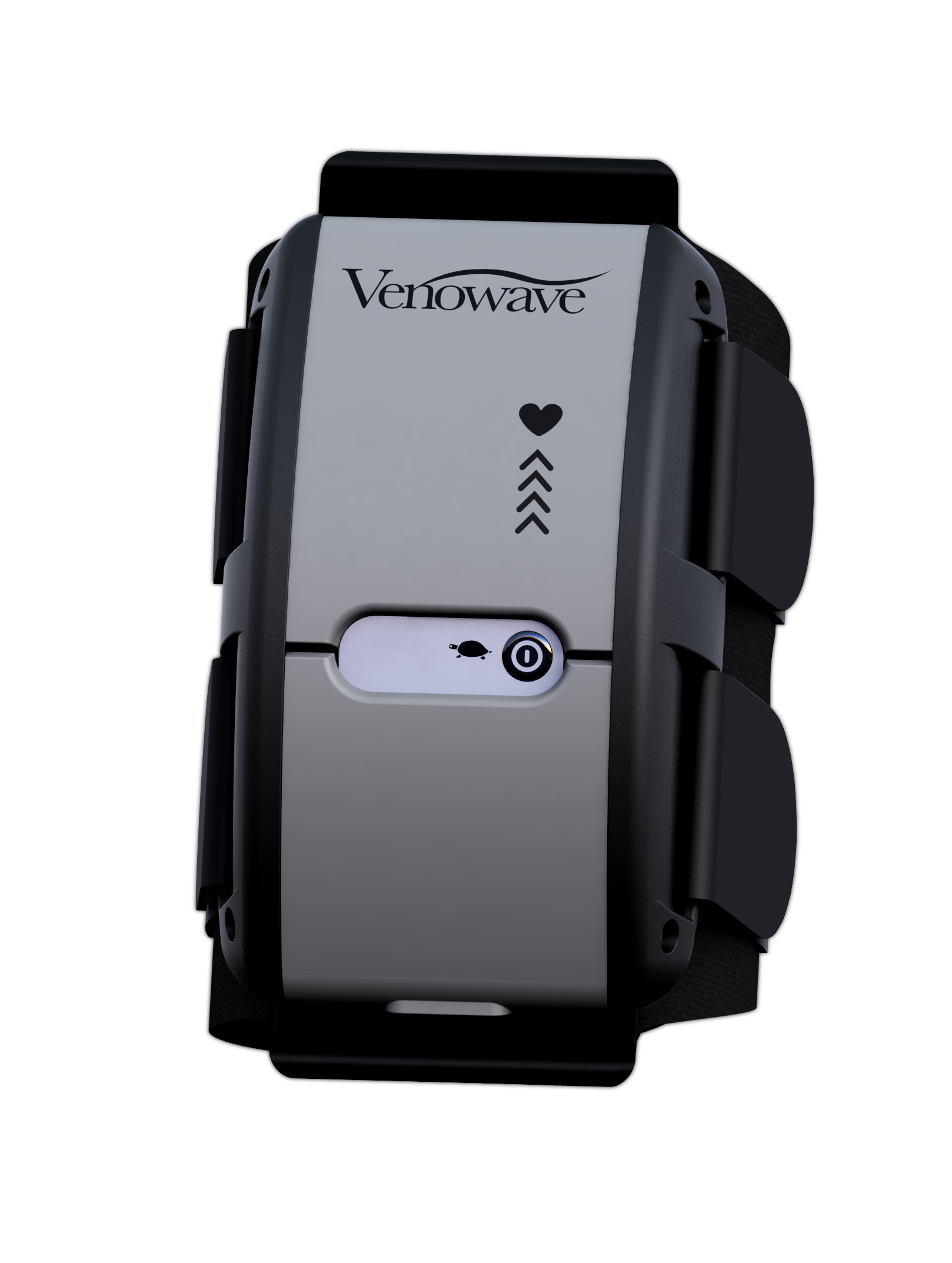
1. The new Venowave wrap combines multiple components (Straps, buckles and wrap) into one. It is easy to use and patients can put it on and take it off without the need of external help.
2. The new device features clean lines and smooth surfaces that are easy to clean and disinfect.
3. The new housing protects the user and other personnel in contact with the device from moving parts and possible pinch-points.
4. The device is visually appealing and appropriate for use inside as well as outside hospital.
5. Space within the housing was used to include an extra battery. This change, as well as other small improvements, more than doubled the battery life of the device.
6. Extensive life testing was conducted to identify the components that failed earliest. The new design includes a slightly bigger and more durable gearbox for the electric motor, as well as stronger plastic pinions and gears inside the actuator unit.
7. Costly components difficult to manufacture were eliminated and replaced with injection molded parts. The new design is significantly better in terms of manufacturing cost-efficiency.
8. Documentation compliant with ISO 13485 was developed and is maintained on a cloud Product Life-cycle Management (PLM) software solution.